top of page
Click photos to enlarge picture and text.
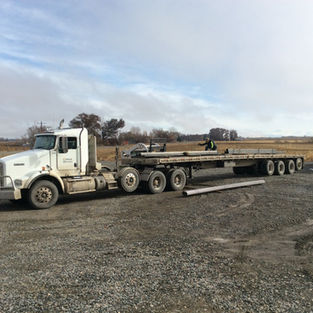
It all starts with a load of steel from Billings MT.

Once the steel is off the truck we load it into our steel rack.

Steel on the steel rack and ready for the saw.

As with most metal shops, the sawing is the first step to the build.
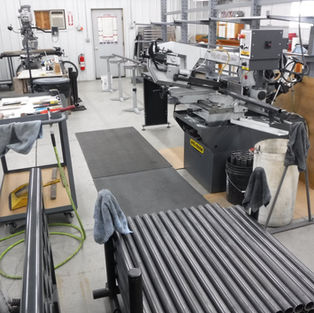
Cutting the legs to length.
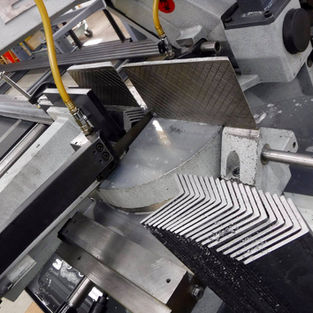
Sawing the frame parts.

Sawing the angles on the frame parts.

All the sawed parts either go to the lathe or the mill next. Here we are turning the ends of the legs after they are welded.

Facing and chamfering the sockets.

Turning the leg cap welds.

All parts in our shop are deburred by hand.
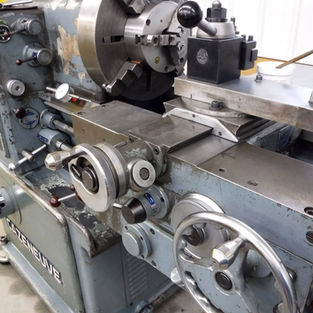
This Cazeneuve lathe is a great machine, they literally do not make them like this anymore.

Our mill, a Bridgeport.
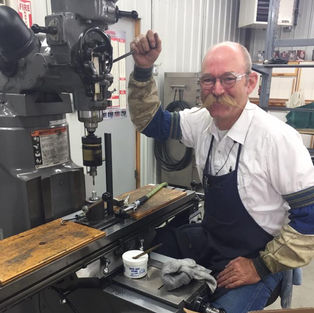
Using a Tapmatic to form threads in the leg caddy pillars, 1/4 - 20 threads at 900 RPM.
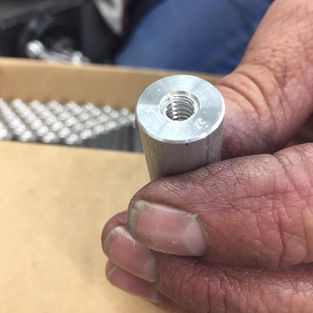
Formed threads are used in the caddy pillars.

Milling the 70 degree end on the frame parts.

60 degree saw cuts ready for milling.
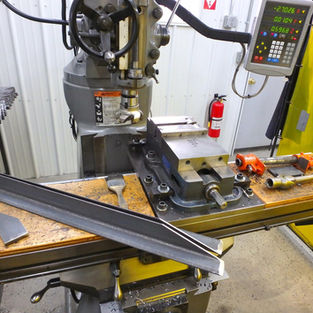
A pair of frame parts after milling.

The slot in the sockets is hand beveled to assure years of smooth operation.
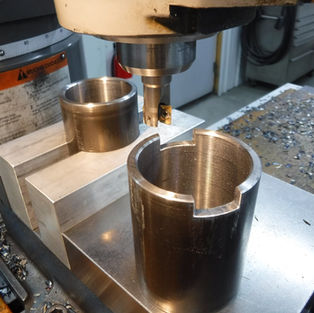
A socket after being beveled.

Beveling leg caddy plates.
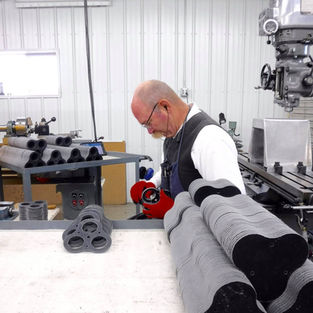
A good audio book is a real plus, when hand beveling the I.D.s on a batch of leg caddy plates.
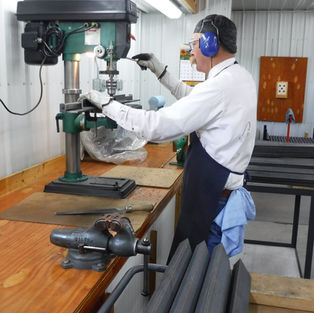
Drilling the mounting holes in the frame parts.
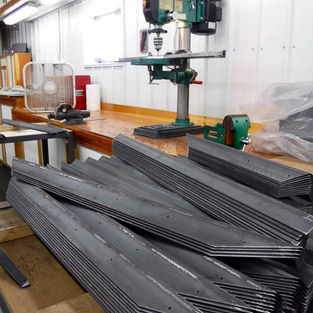
There are 700 holes per build, that Grizzly drill press has earned its keep.

Welding is a large part of a build, each bench has 110" of weld.
bottom of page